Interview in GRAU magazine: 3D-printed formwork from SAEKI — reusable, flexible, and recyclable.
Sustainability in concrete construction: Dr. Leschok in GRAU Magazine about 3D printing and digital production from Switzerland
.jpg)
This interview originally appeared in the GRAU magazine of the Swiss Concrete Products Association (May 2025 issue).
Dr. Matthias Leschok founded the ETH Zurich spin-off SAEKI Robotics AG in 2022. The innovative start-up combines 3D printing with robotics to produce sustainable formwork for custom-made or catalog products. The interview was conducted by Dr. René Jähne, Technology Transfer Officer at the National Center of Competence in Research Digital Fabrication (NCCR Digital Fabrication).
Dr. Leschok, could you give us an overview of the idea behind SAEKI Robotics AG and what prompted you to found a start-up?
SAEKI Robotics AG was born out of the idea of simplifying the cumbersome and cost-intensive planning and production process for special formwork using 3D printing. We wanted to enable more material-optimized concrete components, such as ribbed slabs, to be used. With robot-assisted production, we can convert digital designs into physical components. In this way, we want to make the production process more efficient, resource-saving and flexible, while at the same time increasing design freedom.
But it was certainly a long way until the solution was ready for the market...
During my time at the NCCR Digital Fabrication at ETH Zurich, I was able to see how promising research approaches in architecture were technically feasible but rarely used in practice. This led me to the question: “Why don't these innovative technologies find their way into industry?” Many developments remain in the academic environment, as the appropriate interfaces to planners and construction companies as well as business models are often missing. This is where SAEKI comes in: With our solution, we are building a bridge between research and practice by bringing together digital planning and automated production in an integrated process. My co-founders and I have identified an urgent need for tailor-made components in architecture, construction and industry. By combining robotics, digital fabrication and AI-supported process optimization, we enable the competitive implementation of special solutions and want to usher in a new era of production. In this way, we want to contribute to a more sustainable and efficient construction and production industry.
What distinguishes your printing technology from conventional production methods for formwork and why is it particularly interesting for Swiss concrete prefabrication?
Our patented printing technology is based on an additive, robot-assisted manufacturing process in which material is only used where it is structurally required. In contrast, conventional methods such as disposable wooden formwork often involve manually processing large quantities of material, which leads to a lot of waste, limited design options and higher costs. With our 3D printing approach, we produce project-specific formwork that enables, for example, material-optimized concrete structures that are more cost-effective, more accurate and more sustainable when used multiple times. In addition, our formwork is made from a plastic that can be recycled multiple times and enables a high level of repeatability in the production of concrete parts thanks to its high rigidity and strength. This is particularly interesting for Swiss concrete prefabrication, as it combines high quality standards with a pronounced environmental awareness. Producers benefit from lower material and energy costs as well as shorter production times, making the manufacture of special shapes competitive.
How can your technology be integrated into the existing production processes of Swiss concrete prefabricators?
Our technology can be integrated into existing production processes in various ways. We can replace complete formwork systems for standard products in large quantities or combine individual elements with 3D-printed inserts. We are also able to produce special components or prototypes of formwork for new products. We usually start together with our customers after joint discussion in order to be able to offer a customized solution. We produce prototypes and sample components and use these concrete examples to find the best approach. Once a product has been defined, our customers can easily order future formwork online via our SAEKI portal. After the formwork has been used on the construction site or in the precast plant, we have the formwork collected on site and recycled by a partner in Switzerland, whereby our customers receive a discount on their next order.
How much time and money should companies expect to spend compared to previous processes?
The costs and the time required vary depending on the project and can hardly be specified in general terms. It is important to us not to necessarily print everything in 3D, but to work out an elegant, efficient and cost-effective solution with everyone involved. Our prices are comparable to other processes in non-standardized formwork construction, but our 3D-printed formwork can be used multiple times, which reduces costs in the long term. Thanks to our robotic production systems, which can produce large-format components around the clock, we are also able to deliver larger orders on time and adapt flexibly to different project requirements.
Can you give us a concrete example from practice in which your formwork has already been successfully used for sustainable construction?
An illustrative example is our project with CREABETON AG, which used our additively manufactured formwork for the Tor Alva (White Tower) project in Mulegns. There, we were able to produce particularly geometrically demanding formwork with our 3D printing process and avoid the time-consuming and cost-intensive production of disposable wooden formwork. Thanks to our 3D printing approach, we reduced the amount of material used by around 40 percent and accelerated the construction work at the same time. It also proved that our formwork consistently meets the high surface quality requirements, even when large components are repeatedly cast - a key criterion in this project. Thanks to close coordination with the companies involved and precise digital planning, implementation went smoothly. The consistently positive feedback from this practical application has confirmed that our production method is not only more sustainable, but also economically attractive.
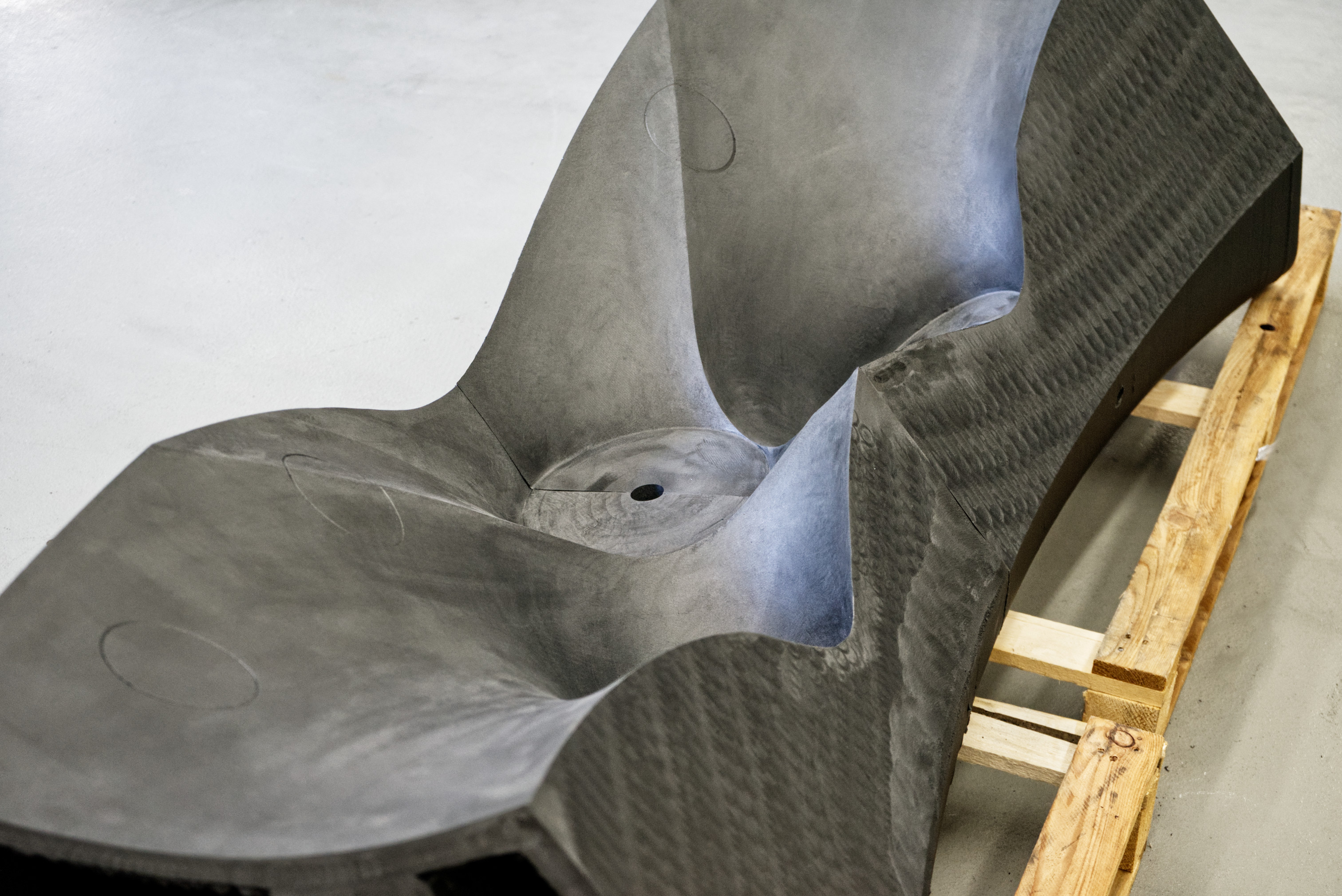
.png)
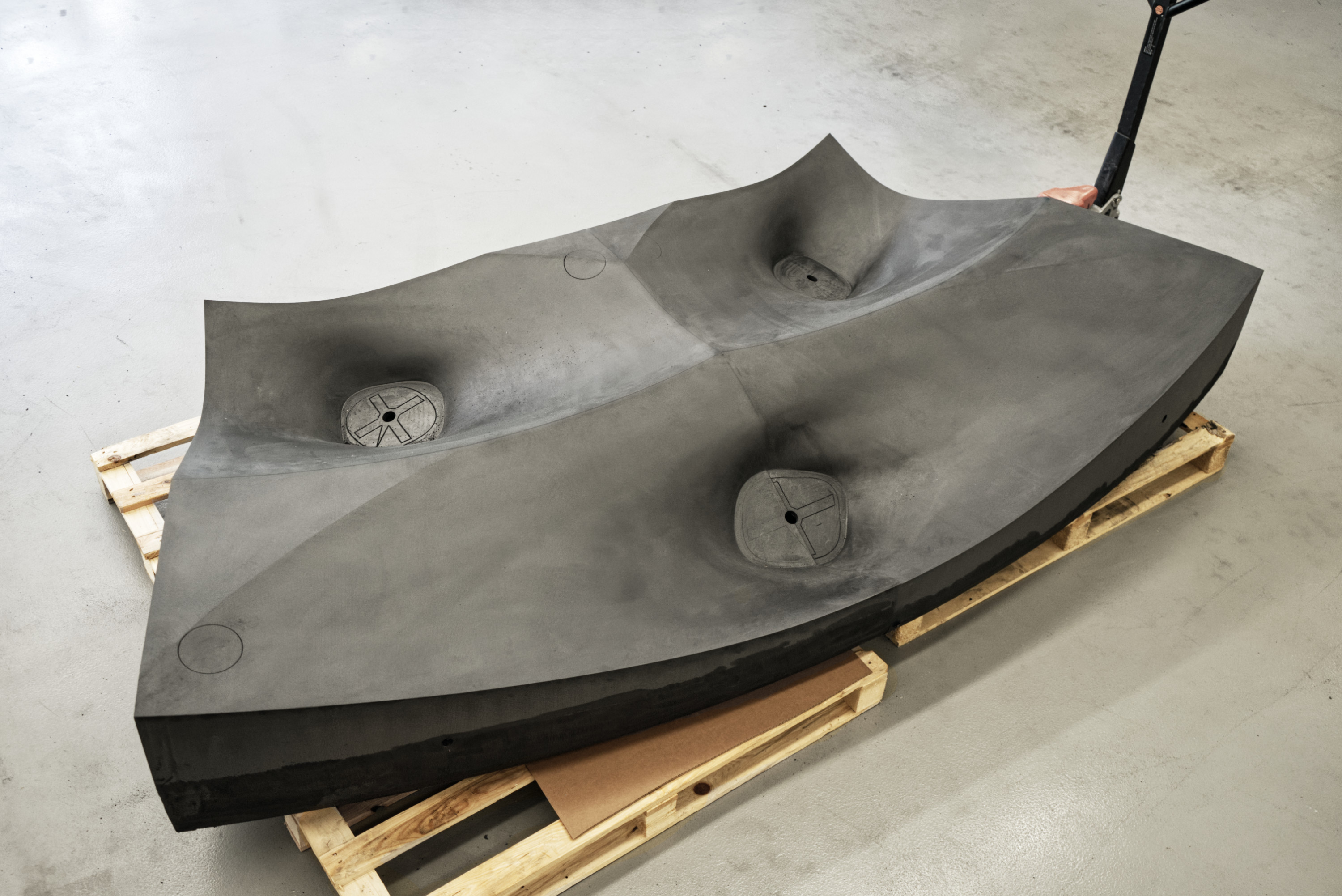
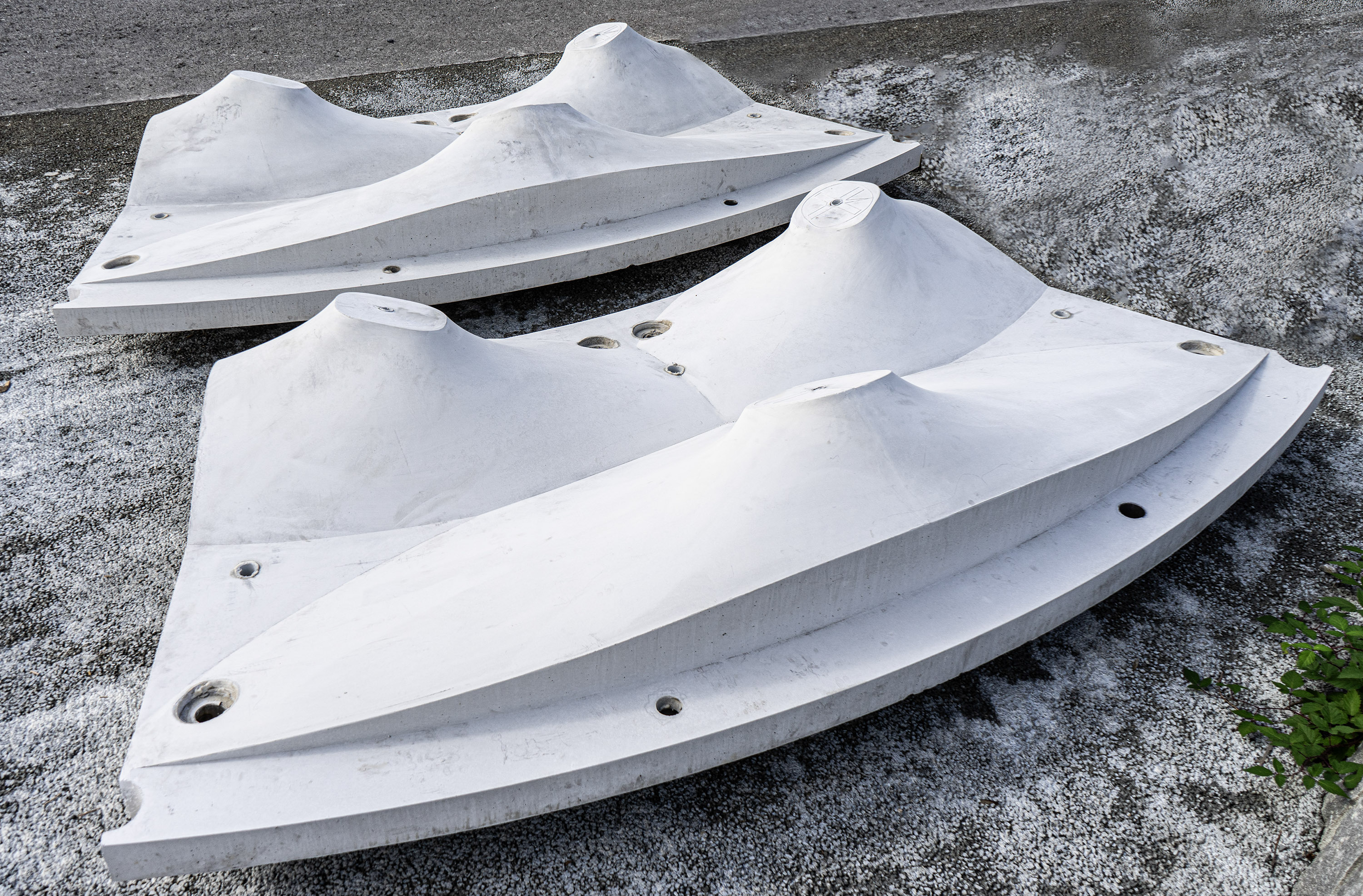
What obstacles did you have to overcome during commercialization, especially in view of the high standards for exposed concrete?
One of the biggest challenges was gaining the trust of construction companies and concrete prefabricators, who often rely on tried-and-tested production methods and tend to be skeptical of new technologies. By gradually providing validated proof of the load-bearing capacity and surface quality of our plastic formwork, we were able to overcome these reservations. Close cooperation with industry specialists also helps us to seamlessly adapt the integration of our production to customers' existing processes by offering a digital process chain from order to delivery. Although this persuasion work was time-consuming and resource-intensive, it was crucial to mastering the transition from research to the market and thus the successful realization of the first construction projects.
Apart from the cost savings: What long-term benefits do you see if concrete prefabricators start using your innovative formwork systems today?
Those who already rely on our formwork systems today will benefit in the long term from better planning and faster response times to changing customer requirements. Thanks to the additive manufacturing method, there is unprecedented freedom of design, as even complex and freely shaped components can be realized without a great deal of additional effort. This innovative character strengthens the competitive position of concrete prefabricators, enabling them to establish themselves as pioneers of sustainable construction methods. Reduced material consumption and lower energy requirements also improve the environmental balance. At the same time, the digital process chain opens up new possibilities for precise planning and documentation, which facilitates quality assurance. In addition, our technology provides a basis for future developments in robotics and automation, so that precast plants can adapt flexibly to changing market and customer requirements in the long term. And finally, Swiss precast concrete manufacturers can distinguish themselves as innovative employers and thus gain a competitive advantage with regard to the shortage of skilled workers and vacant apprenticeships.
To what extent do small and medium-sized companies in Switzerland also benefit from your technology, or is it primarily tailored to large production companies?
Our technology is particularly beneficial to small and medium-sized companies because they don't have to make expensive purchases and can obtain the formwork directly from us instead. This allows them to avoid high fixed costs and benefit from the advantages of additive manufacturing, such as the efficient use of materials and flexibility in design. As we also manufacture formwork in smaller batch sizes, SMEs can implement individual orders quickly without having to plan for long lead times or large storage areas. Our digital planning also makes it easier to coordinate with the customer, which simplifies project management for smaller teams. This customer-oriented service approach is proving to be ideal in Switzerland in particular. It enables them to implement innovative projects with low investment and remain competitive in an increasingly demanding market.
Dr. Matthias Leschok
Dr. Leschok, who holds a doctorate in architecture, has been co-founder and COO of SAEKI Robotics AG since 2022. The company, based in Bäretswil in the canton of Zurich, manufactures recyclable formwork for columns, façades, ceilings and stairs, for example, and currently employs 19 people. Before and during the founding of SAEKI Robotics AG, Dr. Matthias Leschok completed his doctorate at ETH Zurich and gained professional experience in the architecture industry.